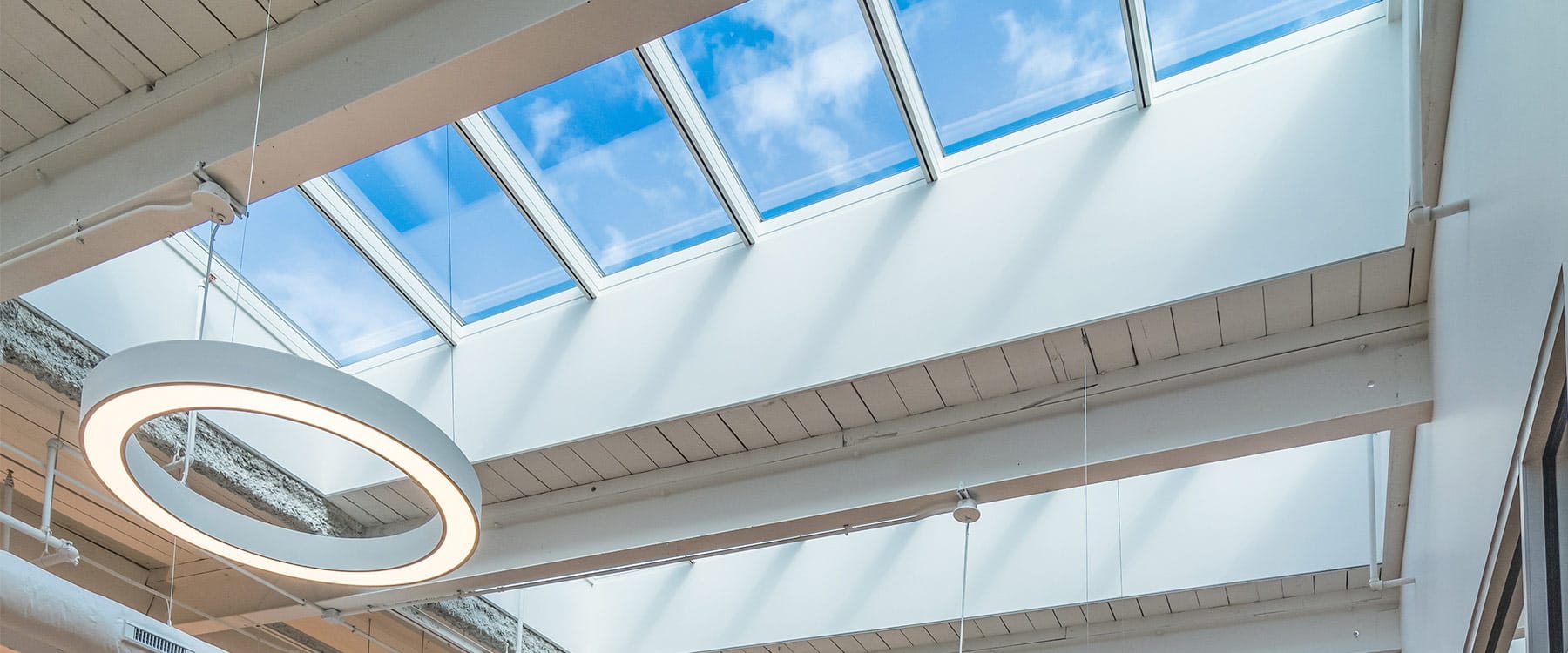
Background:
The historic Beaumont Mill is deeply rooted in the city of Spartanburg in South Carolina’s Piedmont region. The mill produced cotton textiles and consisted of two large, two-story brick buildings constructed parallel to each other between 1890 and 1910. As textile manufacturing technology changed, so did the mill and, at one point, the two structures were connected to create one massive manufacturing facility.
The mill was shuttered in 1997, but with generations of Spartanburg residents having worked within its walls, the community had a strong desire to preserve it. Spartanburg Regional Healthcare System, decided to renovate the building as the new home to its administrative departments, which previously were located in separate buildings around the city.
“We worked to preserve the integrity of this historic building by including the original floors, exterior brick and expansive windows,” said Ken Meinke, Spartanburg Regional Healthcare System's Chief Financial Officer. “The mill’s long history was incorporated into the renovations and we have historic photos and items displayed in the building.”
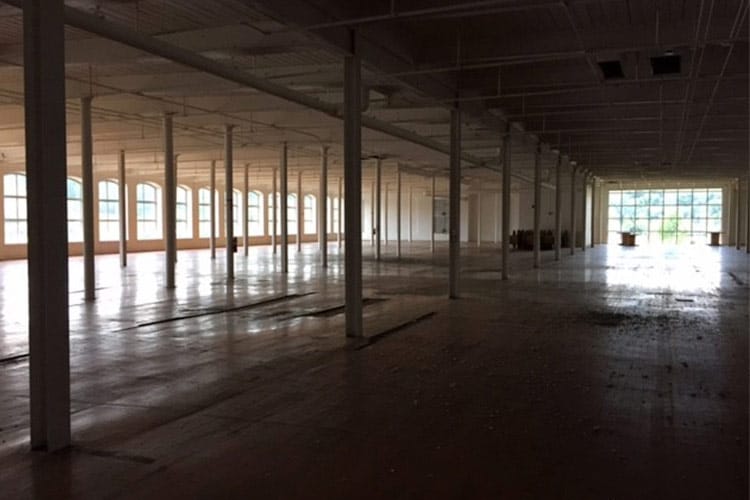
Challenge:
When the two original buildings were connected, it created a deep, dark space.
“From an architectural perspective, being a corporate office and knowing that people would be in the building for long hours, we were concerned about daylight,” said Sara Robinson, the architect with McMillan Pazdan Smith Architecture, who oversaw the project. “Light from windows along the exterior wall didn’t penetrate very deep.”
The architects knew skylights would be an ideal solution both on a functional and a symbolic level by placing them in the roof over the space that connected the two original buildings.
“We made the joining space a central hub defined by natural light from the skylights,” Robinson said. “We symbolically divided the space to reference the original two buildings and by cutting light wells in the second floor, daylight extends all the way to the ground floor.”
Interior walls have storefront windows, allowing light from the skylights to spill into adjacent offices.
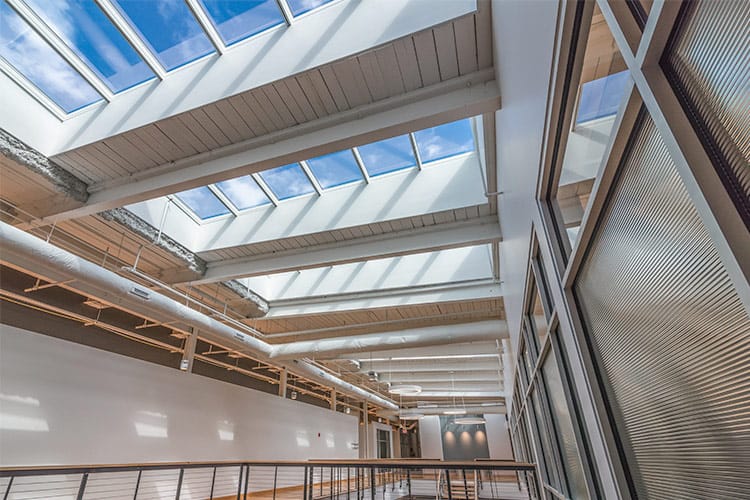
Solution:
The VMS system was the most cost-effective skylight solution for the project in terms of product price, and labor and time needed for installation.
The architects were able to use a standard size skylight unit, rather than special ordering custom units, even though the former mill building has somewhat irregular roof structure dimensions.
“We had columns 9 feet apart in one direction and 26 feet apart in the other direction, but being an old mill building everything was irregular: sometimes the columns were a little over 9 feet apart,” Robinson said. “The VELUX design team was good at looking at each opening to make sure we got the best fit. The standard size skylight unit fit and that helped to save money.”
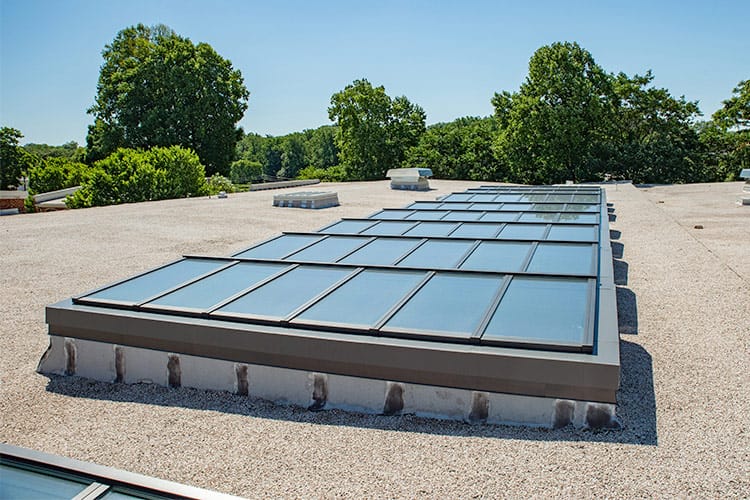